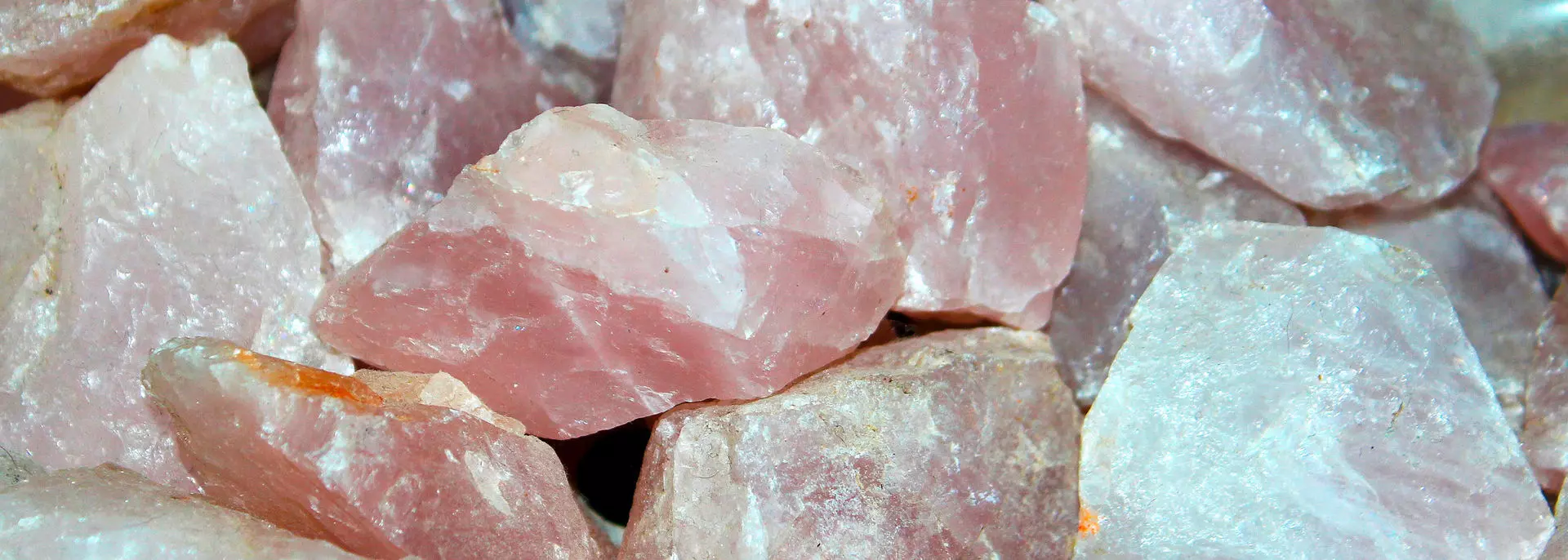
Powders origin from hard minerals as zircon sand, silica, quartz or feldspar have been used in the glass and ceramics industry for centuries. Both the technology in standard applications in the glass and ceramic industry and in high-tech applications in the electronics industry or special ceramics have changed dramatically in recent years and require ever finer powders with special particle size distributions, in particular narrow distributions.
Furthermore, the particle shape of the particles often plays an important role in the application. Wear on the grinding and classifying equipment, the longest possible service life, fast and cost – effective maintenance, the lowest possible specific energy input and the lowest possible contamination are further decisive criteria that must be taken into consideration. All this must and can be taken into account today by the use of various grinding and classifying systems of the Hosokawa Alpine for hard materials.
Hard mineral powders
for standard and high-tech ceramic applications, glass industry or as a filler in special uses
The classical grinding process for hard materials in the field of application of the glass and ceramic industry has always been dominated by the ball milling process. However, thanks to the availability of wear-resistant high-performance air separators, this dry grinding technology can now penetrate into much finer particle sizes of up to d97 = 3. In addition, the technology of ball milling in the medium range of d97 = 20 – 100 microns still have its strengths, as being robust and having low maintenance and wear cost. The ball milling methods have been continuously adapted and optimized in recent years to meet all requirements for hard material processing. By using a combination of different air separators and screening systems, it is possible to adapt an ideally desired particle size distribution to the increased application requirements. So today very narrow grain distributions are e.g. produced for LCD Glass in the TV or mobile phone range or are being split from a standard powder two high quality products that are used as a glaze and the other in the ceramic body and thus each cause a significant improvement in quality.
In the fine range of d97 = 3 – 20 μm, today’s closed-circuit ball mill systems enable low-cost production, especially in comparison to wet grinding processes that are often still in use.
By means of jet milling, largely contamination-free ultrafine powders with steep particle size distribution are produced.
- Processes with low specific energy consumption
- Low wear and maintenance costs
- Influencing the desired particle size distribution
- Ensuring a constant and consistent grain distribution
- Perfect top cut limitation
- Leadership in fineness and quality
- Use of state-of-the-art machine diagnostics – Predictive maintenance
Zircon Sand
Zircon, also known as zircon silicate (ZrSiO4), is found in ancient mineral sand deposits and is typically brown in color.
Zircon is one of the two core product streams from ‘mineral sands’, the other being titanium minerals. During mining, these minerals are separated and removed from their ore deposits.
Zircon sand is mainly used in the ceramics, specialty casting and various refractory applications. Its resistance to high temperature and abrasion makes it extremely valuable in manufacturing processes.
The main use of zircon sand is its conversion to zircon flour, a highly valued product which is used to strengthen concrete and glass properties and refractory bricks. It helps produce pigments and glazes for tiles and sanitary ware by increasing the opacity and brightness of the glaze.
Zircon Flour is manufactured by milling zircon sand, usually in ball mills, either in the dry state or in a slurry. For high quality, ultra-fine, zircon flour powder production, Hosokawa Micron Powder Systems offers the Alpine Super-Orion Ball Mill in circuit with an Air Classifier. For high brightness applications, the ball mill will typically be constructed with aluminum oxide media and lining.
The most common type of Hosokawa Air Classifier used for Zircon Flour is the Alpine Stratoplex (ASP) which is used for a cut point (top size) of 20 to 200 microns. For super-fine applications, the Alpine Turboplex (ATP) Air Classifier is used, with a cut point (top size) of 5 to 50 microns, with single and multi-wheel options. Both classifiers are made with aluminum oxide classifier wheels, and with interior Aluminum Oxide tiling for both fine grinding and durability.
Technology for production
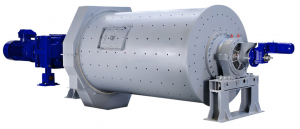
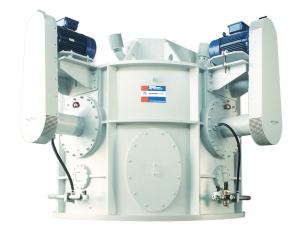
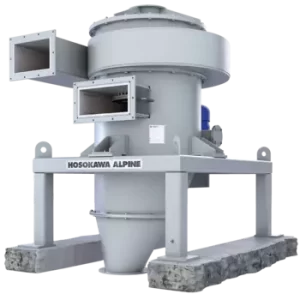