The following is an introduction of the production process of lithium cobalt oxide LiCoO2 LCO, which is one of the leading cathode precursors of lithium ion secondary batteries. The following process can be utilized for not only lithium cobalt oxides, but for a ternary system such as Li(NiaMnbCo1-a-b) NMC and Li(NiaCobAl1-a-b)O2 NCA as well as a quaternary system which is an active material made up of a complicated chemical composition. We will also introduce our technology which can be utilized in the production process after the calcinations process of precursor synthesis (2.1.3 precursor material).
Disintegration Synthesized cobalt based materials have a tendency to become larger in particle size due to the neck growth between particles. From this occurrence, the following problems arise.
- Efficient turnover of the lithium ions from the interior of the particle becomes difficult.
- The packing ratio decreases when coated onto the aluminum foil of the electrical current collector.
- Increase in the unevenness of the coated surface.
To relieve the following problems, the material needs to be ground to roughly 10-30μm. However, since the increase of fine particles has a negative effect on the flowability and slurry viscosity, it is essential to produce powders with the most suitable particle distributions. During the disintegration and grinding process, if contaminations (especially metal contaminations) enter the cathode active materials, it could lead to short circuiting, overheating of the battery from electrochemical reaction, and combustion. Therefore, it is essential to minimize the amount of contamination as much as possible. To fulfill these needs, our grinding units can be manufactured using tungsten carbide as well as coating fine ceramic particles onto the surface of metals to minimize abrasions.
We also have an ACM Pulverizer model called the ACM-HC with powder contact parts made of all ceramic material to promote a metal contamination free grinding process. It is an unit often used within the cathode production line. Hosokawa can offer metal contamination free systems for not only grinding units but for piping and bag filters as well. To increase the conductivity and flowability of the ground powders, processes of additive coating and compacting can be performed using the Nobilta.
Once oxidized, the material is quickly cooled by gases. By mixing multiple solutions before spraying, a multi-composite chemical compound can be synthesized. Multi-component metal oxides can be effectively utilized for additives to cathode materials.
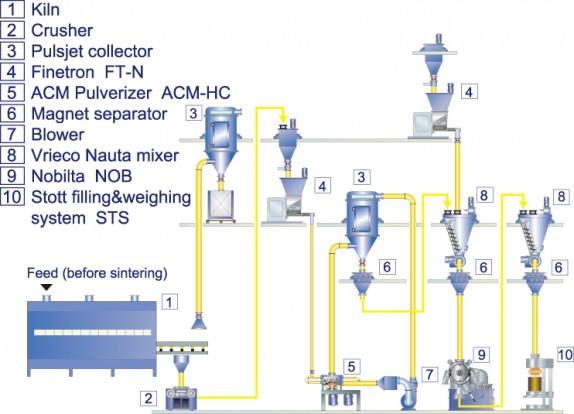
Surface Treatment
Multiple chemicals are coated onto the surface of the active materials to increase charge/discharge capacity, rate characteristics, cycle characteristics, safety, and reliability. For example, reducing the battery’s internal resistance through solidifying carbon black base materials to assist conductivity is a widely used method. Recently, to increase rate characteristics and temperature stability, methods of applying a layer of ceramics to the active material as well as solidifying onto the surface of nano-particles are being used.
These processes perform the sol-gel process, chemical reaction, and the absorption process during the liquid phase, then put through the calcinations process. It requires a drying process which increases energy cost and left-over solutions, having a negative effect on the quality. This passage will introduce the dry process technology of solidifying and coating nano-particles onto the surfaces of sub-micron to micron sized particles.
For surface treatment of cathode materials, the dry process particle compounding unit Mechanofusion and Nobilta are often used. In recent trends, the ceramic type Nobilta is widely being utilized. By coating materials such as Acetylene black particles onto LCO, Aluminum nano-particles onto NCA, Aluminum nano-particles onto NMC, and LiFePO4 onto LiMn1.5Ni0.5O4, not only is the cycle characteristic and bulk density increased, but the amount of solutions required in the next process can be decreased as well
Analysis of the Powder
Analysis of the powder’s characteristics is essential for the powder process and quality control. By installing an online particle distribution measuring unit with grinders or classifiers, real-time quality control of the product size can be performed.
The Powder Tester is used worldwide as a standard unit for quantitative evaluation of the powder’s flowability and tap density, evaluations that would normally greatly differ if operated manually and/or analysis method. Therefore, the Powder Tester can be used for checking the quality of the purchased material, evaluation of the powder being produced for preventing problems that may arise during operation, and quality control of the final product.
In addition, for analysis of wettability and wetting rate which are essential characteristics for determining the pasting process and reactivity of the electrolytic solutions, the Peneto Analyzer is utilized for characteristic analysis of active materials for batteries as well.
Feeding and product collection, filling and measuring, protection of the work environment
In addition to mills and mixers, material feeding devices such as the Finetron, bag filters used for separating and collecting fine particles from the air, Stott hygienic filling and weighing systems for weighing powders while filling, and chemical hazard preventive units such as the safety booth utilized for protecting workers and the environment from hazardous powders, as well as preventing cross contamination for quality control, are important peripheral equipments. When it comes to structuring a battery material production process, it is important to not only put an emphasis on individual process equipments, but to look at the material balance as a whole, including the furnace and sieve equipment. Hosokawa has the strength in advising and offering such production processes.